WaterHQ attended ISK-Sodex in Turkey, capturing the latest market developments in the water industry. One of the hot topics was Industry 4.0. Alkim Gur from Dikkan Group explains how Industry 4.0 has revolutionized valve production. Factories adopting smart production are using smart applications including robots and 3D printers. Manufacturers use the virtual world to draw, design and refine their products, before bringing them into the real world for consumption. Industry 4.0, which is becoming more prominent in Turkey, is offering flexible and fast production with more cost savings and less human error. The process involves capturing data from the physical area, processing progress in the virtual world and feeding it back into the real world.
Industry 4.0 is equivalent to the 4th industrial revolution. Looking back at the timeline, steam engines were the discovery of the 18th C, electrical power and production line rose in the 20th C, automation marked the 3rd industry revolution and internet or cybernetics is bringing the 4th wave of change in industry production lines.
The production processes in Industry 4.0 begin with the customer in mind and every link of the production chain. Internet of Things (IOT) involves bringing together all the elements of a process that can communicate together, big data is produced, collected and analyzed as a result. All aspects of the production line is pertinent for evaluating and analyzing values, that are reintroduced into the system and stocked in cloud. End users operating the machine are able to activate and repair it independently, using the information made available.
At the production level simulations are created in a virtual area and translated into physical life for software integration. IP systems are used to connect all levels of the industry, with real time connection provided for all stakeholders. Information is made available for progression at every level, defined and fed back into the system.
Smart factory application involves robots, known as cobots that learn about the process and communicate with people. 3D printers are cost effective and ensure fast production, where errors are pinpointed and eliminated (useful for R&D); these are great attributes for entering new markets. Businesses can harness the power of Industry 4.0 to suit their specific needs and evolve.
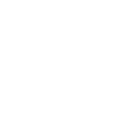
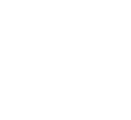
When the elements of a valve are brought together for production, the subject is split into 3 parts; the output of the process that forms part of the input in another process and finally the end user. In a smart factory the system of filtering involves monitoring internal and external pressures of the inner filter, preventing cavitation. A smart product will read the existing conditions and automatically implement the necessary changes in the filter.
Smart production involves smart carrying systems used in the raw material warehouse, eliminating any time losses during the process, a method already being used in the retail industry. All drawings are done within the system to eliminate human errors and all information is retrieved independently by the robot from the system, with no human intervention. The digital production line is transferred into the virtual world for casting and testing, and once validated it’s transferred into the physical environment for successful design and consumption.
Once the valve is produced, the benefits are reaped in the new production line. Pressure sensors are inserted to monitor the exit pressure and ensure all flow is controlled. Potential complications are transferred to a virtual platform, where issues are followed up with and resolved. This prepares manufacturers for any potential breakdown during consumption.
waterHQ Staff