Water is an essential raw material for manufacturing of paper boards, and effluent treatment is critical part of this process. Wastewater is characterized by extreme quantities of pH, total dissolved solids (TDS), total suspended solids (TSS), biochemical oxygen demand (BOD), and chemical oxygen demand (COD).Â
Produced wastewater from the paper boards industry has detrimental impacts on the environment and poses a serious threat to wild and human life. The pulp and paper industry is ranked as the third world's largest consumer of water and is consequently producing high amounts of wastewaters.
The environmental impact of pulp and paper industry is a particular concern since these units generate 150- 200 m3 effluent/ton paper with a high pollution loading of 90-240 kg suspended solids /ton paper, 85-370 kg biochemical oxygen demand (BOD)/ton paper and 500-1100 kg chemical oxygen demand (COD)/ ton paper and it is sixth largest polluter in the world (after the oil, cement, leather, textile, and steel industries) and emits a variety of gaseous, liquid, and solid wastes to the surroundings.
Activated sludge processes can achieve high removal efficiencies for BOD and COD. The biological treatment process is able to reduce COD, BOD, and toxic low molecular weight derivatives. The pulp and paper industry uses conventional activated sludge treatment process in which they are using nonspecific micro-organisms and keep food/microbe (F/M) ratio low in the aeration tank.
Effluent treatment plant components
The wastewater generated from pulping process contains high concentration of BOD, COD and TSS. The ETP comprises of the following units, viz. drum screen, sedicell, equalization tank, primary clarifier, conventional Aeration, secondary clarifier - A, extended aeration, secondary clarifier - B, tertiary clarifier, chlorination, milt grad sand filter and mechanical dewatering devise (MDD).
The activated sludge plant treats an average of 4000 m3 wastewater per day. The effluent is first passed through screened with coarse filters (bar screen), and followed by dram screen for removal, of plastic and other floating materials in the pre-treatment stage.
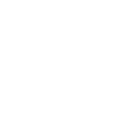
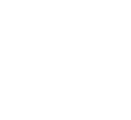
The effluent pumped into sedicell fiber recover system with addition of flocculent (4 kg/d) to remove the bottom and top of flotation pulp with 6-7 par presser of air dissolving tube (ADT) system and output of effluent less than 50 ppm of TSS.
In conventional aeration tanks, added nutrients for microbial activation purposes and surface aerators are provided in aeration basins for oxygen transfer and mixing of biomass with wastewater. This aerobic biological treatment process is where the bacteria decompose the organic matter in presence of oxygen.
A diffused aeration arrangement provided at the periphery of aeration tank will ensure mixing of sludge every once in a while. In clarifiers, solids get settled at the hopper bottom. The supernatant from the clarifier overflows uniformly over the peripheral launder.
Effluent from secondary clarifier-B shall be entering into the accelerated gravity separator. The sludge generated from primary treatment and biological system taken sludge produced in the process are taken to the belt press dewater well be routed back to the treatment system. The high costs associated with the plant and their operations require a wise optimization of the process.
In recent years various systematic design approaches to wastewater reuse across complex manufacturing operations have been developed. Because economic benefits are undoubtedly a major driver for industry to implement wastewater reuse programs, recent research in this area has focused on the economic optimization of wastewater reuse systems.
Present research is to treat the paper board industry wastewater in biological oxidation by means of environmental friendly manner and also to know the influences of Temperature, pH, F/M ratio and DO concentration on the microorganism's growth and pollutant removal and to assess the biodegradability of the wastewater and also to recycle and reuse the waste for economic profits and suitability of a zero discharge system to the paper board industry.