Water pollution degrades surface waters making them unsafe for drinking, fishing, swimming and other activities. In an effort to improve these waters, stringent discharge limits often are enacted to ensure that water released into the environment (rivers, lakes, ocean, wetlands, etc.) meets strict dissolved oxygen (DO) criteria. Utilities frequently have the added difficulty of keeping DO levels in compliance due to seasonal storm events, unusually high temperatures or treatment plant operational upsets. To meet today’s required DO standards, post-aeration has become a critical process at most wastewater treatment plants.
A wide range of technologies can be harnessed to oxygenate water including cascade aeration, spray aeration, bubble diffusers, pure oxygen injection and atmospheric air injection. And there are numerous options for the variety of space, management, energy, and cost requirements that exist. With growing targets and shrinking budgets, an increasing number of wastewater treatment professionals are opting to use the uncomplicated Mazzei Pipeline Flash Reactor™ (PFR) with sidestream venturi injection which facilitates the most efficient, cost effective, inline gas transfer process possible.
In a PFR system, ambient air is drawn into a sidestream flow—a flow of just 3 to 5 percent of the total discharge volume—and is highly oxygenated through the use of a venturi injector. The injector harnesses the pressure differential of flowing water to draw in atmospheric air which is then mixed into solution. The oxygenated sidestream flow then enters the Pipeline Flash Reactor where additional mixing and contacting is achieved via the PFR’s Mass Transfer Multiplier™ (MTM) mixing nozzles. The Pipeline Flash Reactor heightens the shearing of the entrained bubbles which maximizes the gas-liquid interface initiated by the venturi injector.
The use of the PFR essentially amounts to inserting a flanged spool of pipe into the main pipeline flow to replace or enhance an entire contact basin. Mazzei engineers design PFR systems for specific project sites and conditions. Such customization is especially crucial for retrofit projects. One key advantage of the Pipeline Flash Reactor is its small footprint/low infrastructure requirement.
Hancock County Wastewater Treatment Plant
An example of the PFR’s key features in action can be found at a municipal wastewater treatment plant in Hancock County, Mississippi, USA. The design engineers had a pressurized effluent line that was to discharge into a local river. Since the line was pressurized, the standard method for increasing DO—a cascade (aka waterfall)—was not a valid option. They opted instead for PFR technology. This technology creates a simple, powerful aeration system that fits on a skid and provides maximum transfer of oxygen with the lowest possible energy usage and minimum operator involvement.
The Hancock County aeration system includes four air injection skids, each consisting of a booster pump, a 2-inch venturi injector, pressure gauges, a control panel, and a PFR. The PFR is merely 40.64 cm in diameter and 121.92 cm in length and causes little to no pressure loss. As a result, the utility is able to pack a pond’s worth of aeration into just over 121 cm of pipeline, with minimal added energy costs—no blowers required for the oxygenation of this secondary effluent.
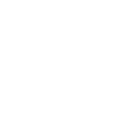
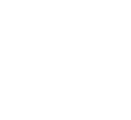
In this new system, a fraction of the mainline flow is taken off the effluent pipeline, directed through a booster pump, and then through a venturi injector to draw in and aspirate ambient air.
The aerated sidestream is then mixed back into the effluent pipeline through the four MTM mixing nozzles within the stainless steel PFR for final oxygen transfer and uniform mixing, eliminating the need for an additional tank/basin and drastically reducing the energy consumption and footprint.
The aeration system control panel is designed to run the injection skid pump (which drives the aeration system) based on the plant load levels when the wastewater treatment plant effluent pumps are operating.
The Hancock County Wastewater Treatment Plant was started-up in August 2010, and has been meeting discharge DO limits with no problems. The plant operators, who are responsible for maintaining several plants in southern Mississippi, appreciate the minimum maintenance and low operator involvement that this system requires.
Mazzei’s aeration systems have proven to be a simple solution for this facility and others. With Mazzei’s fluid design capabilities, Mazzei is able to build a system to meet the specific needs of each individual project resulting in efficient and effective results every time.
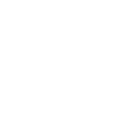
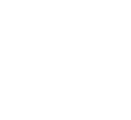
Efficiency in energy and space
The Pipeline Flash Reactor system’s only energy demand is a pump large enough to push the sidestream through the injectors and PFR, since the PFR section of the pipe in itself has negligible head loss. The PFR’s energy demands stand in significant contrast to the high energy demands of blower systems or bubble diffusers in large ponds or lagoons as well as those of pump systems that must overcome the pressure drop often seen downstream of static mixers.
Energy demands for the PFR may be further refined through the use of dissolved oxygen meters installed downstream, which can control the volume and pressure of the sidestream flow to match oxygen levels with system needs.
The PFR provides a controlled and stable mixing environment. In contrast, massive volumes of water in ponds, contact basins, or tanks are much less responsive and more difficult to control with precision—they must be maintained to much higher DO levels to accommodate for areas that experience high rates of loss, areas of poor mixing and dead zones.
Because all mixing takes place inside the venturi injector and the Pipeline Flash Reactor, PFR systems eliminate the need for mixing basins or tanks as well as the space and structures needed for blowers, diffuser grids, large pumps, and other infrastructure.
In new projects, this advantage makes the PFR technology an excellent option for reducing capital costs in real estate, engineering, and construction materials.
It also makes a PFR system an extremely efficient option for retrofitting existing treatment facilities faced with the need to replace aging systems or comply with new DO standards. Once installed, Pipeline Flash Reactors and venturi injectors are essentially maintenance free. The fact that many PFRs are buried after installation offers evidence of confidence in their reliability and such a practice provides an excellent way to further reduce their physical footprint. In the words of one wastewater treatment manager, the Pipeline Flash Reactor system is “the most elegant, and probably the most cost-effective, solution out there.”